Contents
Preface
The railway civilization, having evolved for more than two centuries, not only serves as a testament to its pivotal role in the history of land transportation, but also lays a crucial foundation for the modernization of nations worldwide. As technology continues to progress at an unprecedented pace, railway trains are propelled to ever-increasing speeds, giving rise to a growing demand for passenger safety. As a result, ensuring the simultaneous prioritization of safety and efficiency in railway-related equipment remains a paramount concern for equipment manufacturers.
The modernization of railways has given rise to a multitude of electronic devices that serve various functions, such as sensor systems for monitoring railway operation safety, air conditioning equipment, lighting devices, door control systems, railway communication systems, and highly-sensitive sensors, among others. These electronic devices rely on power provided by batteries installed on the railway.
Due to the prolonged exposure to railway vibration, all electronic devices face unstable voltage for extended periods. Additionally, considering the substantial safety concerns involved, all railway electronic equipment must adapt to adverse environmental conditions such as varying altitudes, humidity levels, presence of oil and gas, impact, vibration, temperature, and voltage. Such equipment must provide optimized performance to meet the strict requirements of railway applications.
However, the vehicle battery system is typically located at the front or rear of the train, necessitating the transmission of voltage through long cable lines to the electronic devices or systems. During the transmission process, electromagnetic interference is prone to occur, including transient voltage spikes caused by nearby lightning and fluctuations in power lines. The train battery must also drive starter motors, pumps, compressors, drivers, relay coils, switch devices, AC generators, generators, transformers, and other high-power load equipment. These factors often result in an unstable, highly fluctuating, and noisy power supply, which can lead to electrical shock and potential hazards, such as transient voltage spikes, mechanical damage, ignition, fires, as well as gaps, arcing, and short circuits in the PCB circuitry due to grounding loops. Since it exposes electronic equipment or systems to significant impact and failures, it becomes evident that railway electronic equipment and systems require high-performance, reinforced insulation, robust, and reliable railway DC-to-DC power modules as essential prerequisites for ensuring the long-term stable operation of trains.
Based on the aforementioned requirements, EN 50155 is the European standard specifically developed for electronic equipment used in railways. Most countries choose to make reference to this regulation as the testing standards cover various aspects, including input voltage, I/O isolation voltage, insulation voltage, electromagnetic compatibility (EMC), mechanics, and reliability tests for harsh environments. These reliability tests include working temperature, cooling, humidity, vibration, and shock testing.
MINMAX not only provides suitable products, but also offers comprehensive services to earn the trust and support of end-users. This includes providing analysis and verification required by customers during the development process using MINMAX products or offering special designs based on customer requirements. MINMAX is dedicated to serving you wholeheartedly and facilitating close collaboration between your company and your customers.
Figure 1-MINMAX's complete range of railway-certified products are all compliant with EN 50155
MINMAX's complete range of railway-certified products are all compliant with EN 50155
To save weight and maximize space utilization in modern and high-speed railways, the batteries on the railway are often charged to 24V, 72V, or 110V. However, most electronic equipment and systems on the railway require input voltages of 5, 12, 15, 24, or 54VDC. Therefore, a railway-certified DC-to-DC power converter is required between the railway battery system and the electronic equipment to convert the DC voltage of 24V, 72V, or 110V to the DC voltages of 5, 12, 15, 24, or 54VDC, which are then supplied to numerous electronic systems.
Taking the railway-certified DC-to-DC power converter for instance, the input side must be connected to the railway battery. Therefore, this standard specifies that the input voltage of the converter must comply with the operating voltage of the railway battery to ensure the normal system operation. Additionally, the testing of transient voltage is also performed to ensure the insulation and resilience of the power module to extreme voltage fluctuation, thereby ensuring the safety of long-term operation.
Regarding the primary insulation barriers for railway DC power architecture, the required DC input voltages of 24V, 28V, 36V, 48V, 72V, 96V, and 110V are all supplied by the railway battery (Vn). Generally, railway batteries do not have voltage stabilizing devices. Therefore, MINMAX's railway-certified DC-to-DC power modules must withstand the following three conditions during operation:
- Voltage fluctuations from 0.7 Vn to 1.25 Vn (refer to Figure 2).
- Voltage drops to 0.6 Vn in 0.1 seconds (refer to Figure 3).
- Transient voltage spike of 1.4 Vn lasting for one second during battery startup process (refer to Figure 3).
Figure 2-DC Power Supply Voltage
Figure 3-Fluctuation Requirements for Temporary DC Power Supply Voltage
Type of tests of EN 50155:2017
The table below shows that the power tests for MINMAX's railway-certified DC-to-DC power converters include input voltage, undervoltage, transient variations, and voltage spikes. Moreover, MINMAX's testing standards go beyond EN 50155 by establishing equivalent or more stringent testing conditions to ensure the long-term stability of the power modules in railway electronic equipment systems.
Type of Test | EN 50155: 2017 (Source of Reference) | |
---|---|---|
Standard Test Levels | MINMAX Test Levels | |
A. Supply Variations | EN 50155 13.4.3.2 / EN 50155 5.1.1.3 | |
Test Voltage / Time: 1.4 VN / 0.1sec. Test Voltage / Time: 1.4 VN / 1sec |
Test Voltage / Time: 1.4 VN / 10min. Test Voltage / Time: 1.4 VN / 60min. Test Number: repeated 10 times |
|
B. Temporary supply dips | N 50155 13.4.3.3 / EN 50155 5.1.1.3 | |
Test Voltage / Time: 0.6 VN / 0.1sec. | Test Voltage / Time: 0.6 VN / 10min. Test Number: repeated 10 times |
|
C. Supply Interruptions | EN 50155 13.4.3.4 / EN 50155 5.1.1.4 | |
Class S1: 100% VN / 0mS Class S2: 100% VN / 10mS Class S3: 100% VN / 20mS |
Class S1: 100% VN / 0mS Class S2: 100% VN / 10mS* Class S3: 100% VN / 20mS Test Number: repeated 10 times |
|
D. Supply Change Over | EN 50155 13.4.3.5 / EN 50155 5.1.3 | |
Class C1: Dip 40% VN / 100mS Class C2: Interruptions 100% VN /30mS |
Class C1: Dip 40% VN / 100mS & 10min. Class C2: Interruptions 100% VN /30mS* Test Number: repeated 10 times |
*Note: If additional components are required to meet the above conditions, please contact MINMAX for more information.
A. Supply Variations
Testing should be conducted to prove that the system operates properly under the rated power supply voltage and within the specified upper/lower limits.
→If the equipment remains functionally operational without any deviation when subjected to a voltage up to 1.4 times the rated supply voltage for a duration not exceeding 0.1 seconds, it shall meets Performance Standard A.
→If the equipment remains functionally operational without any deviation when subjected to a voltage up to 1.4 times the rated supply voltage for a duration not exceeding 1 second, it shall meets Performance Standard B.
B. Temporary supply dips
Voltage dips in the power supply primarily occur due to faults in the DC distribution system or sudden load changes. The testing method involves reducing the supply voltage to 0.6 times the rated voltage (0.6Un) and ensuring that it does not cause any functional deviations within a duration not exceeding 0.1 seconds. If the equipment remains functionally operational without any deviation under these conditions, it meets Performance Standard A.
C. Supply Interruptions
In the event of a short circuit in the DC power distribution circuit, the input voltage may briefly drop to 0V or exhibit a low impedance condition. Interruptions can be categorized into three types:
S1: In cases of voltage interruption, no performance criteria are required. However, the converter should continue to operate as specified after the voltage interruption to meet the S1 specification.
S2: If the voltage interruption lasts for 10 milliseconds without causing any deviation in the converter's functionality, it meets the S2 specification.
S3: If the voltage interruption lasts for 20 milliseconds without causing any deviation in the converter's functionality, it meets the S3 specification.
D. Supply Change Over
The equipment should be capable of smooth operation under the following conditions:
If the rated supply voltage drops to 0.6 Un for a duration of 100 milliseconds without causing any deviation in the functionality of the converter, it shall meets performance standard A.
If the rated supply voltage decreases to 0V for a duration of 30 milliseconds without causing any deviation in the functionality of the converter, it shall meets performance standard B.
EN 50155:2017 Isolation Voltage and Withstanding Voltage Testing
The isolation and withstanding capability of power modules is an important specification that must be taken into account by manufacturers. Using isolated power modules can protect personnel from physical and electrical harm as well as safeguard the backend load equipment and systems. It is an effective method to prevent the spread of faults and plays a crucial role in railway electronic equipment where safety is of utmost importance. Therefore, EN 50155 includes isolation voltage testing as one of the basic test items. Nonetheless, MINMAX internally adopts even higher testing standards to ensure that the product's safety performance meets the higher requirements of customers.
MINMAX's railway-certified power converters have all passed the enhanced 2000VAC isolation/withstanding voltage testing, which is also used to verify the required design in terms of creepage distance, air clearance, and insulation levels of the power modules. The aforementioned standards comply with the limited leakage current under normal/single fault conditions and serve to protect sensitive system circuits from hazards such as noise, electromagnetic interference, power bus fluctuations, electric shocks, surge voltages, transient spikes, insulation breakdown, mechanical damage, fire, clearances, arcs, and short circuits during railway operations.
Type of Test | EN 50155: 2017 (Source of Reference) | |
---|---|---|
Standard Test Levels | MINMAX Test Levels | |
Isolation / Withstanding Voltage Test | EN 50155 13.4.9 | |
Test Voltage / Time: 1500VAC / 60sec. | Test Voltage / Time: 2000VAC / 60sec. |
Figure 4-All MINMAX's railway-certified products have passed the enhanced insulation & withstanding voltage testing of over 2000VAC.
EN 50155:2017 Electromagnetic Compatibility (EMC) Testing
Under the influence of modernization, a wider range of electronic devices consisting of numerous electronic components are installed on trains. In pursuit of miniaturization and lightweight design, integration has become an indispensable capability for electronic device manufacturers. Therefore, ensuring that the devices are not susceptible to interference or do not affect the performance of other equipment becomes crucial, particularly in confined spaces.
As electromagnetic compatibility (EMC) is a significant category in the EN 50155 certification, MINMAX's railway-certified DC-DC power modules adhere to the European Union standard EN 50121-3-2, "Railway Applications - Electromagnetic Compatibility - Part 3-2: integration of apparatus into rolling stock." This standard declares that the conducted and radiated disturbances of the power modules must not exceed the specified limits. Additionally, the modules should remain unaffected by external radiation, surges, electrostatic discharge (ESD), and electrical fast transients (EFT) with a certain level of self-protection capability.
EMC | Type of Test | EN 50155: 2017 (Source of Reference) | |
---|---|---|---|
Standard Test Levels | Standard Test Levels | ||
EMI | Conducted Emission | EN 50155 13.4.8 / EN 50121-3-2, EN 55016-2-1 | |
Frequency / level: 0.15~0.5MHz / 99 dBuV Frequency / level: 0.5~5MHz / 93 dBuV Frequency / level: 5~30MHz / 93 dBuV |
Frequency / level: 0.15~0.5MHz / 66 dBuV* Frequency / level: 0.5~5MHz / 60 dBuV* Frequency / level: 5~30MHz / 60 dBuV* |
||
Radiated Emission | EN 50155 13.4.8/ EN 50121-3-2, EN 55016-2-1 | ||
Frequency / level: 30~230MHz / 40 dB(uV/m) Frequency / level: 230~1000MHz / 47 dB(uV/m) Frequency / level: 30~230MHz / 40 dB(uV/m)* |
Frequency / level: 30~230MHz / 40dB(uV/m)* Frequency / level: 230~1000MHz / 47 dB(uV/m)* |
||
EMS | ESD Immunity Test | EN 50155 13.4.8 / EN 50121-3-2, EN 61000-4-2 | |
Air Discharge: ±8KVDC Contact Discharge: ±6KVDC Indirect Discharge HCP & VCP: ±6KVDC |
Air Discharge: ±8KVDC Contact Discharge: ±6KVDC Indirect Discharge HCP & VCP: ±2/4/6KVDC |
||
Radio-Frequency, Electromagnetic Field Immunity Test | EN 50155 13.4.8 / EN 50121-3-2, EN 61000-4-3 | ||
Frequency / Field: 80~1000MHz/20 V/m Frequency / Field: 1400~2000MHz/10 V/m Frequency / Field: 2000~2700MHz/5 V/m Frequency / Field: 5100~6000MHz/3 V/m |
Frequency / Field: 27~80MHz/20 V/m Frequency / Field: 80~1000MHz/20 V/m Frequency / Field: 1400~2000MHz/20 V/m Frequency / Field: 2000~2700MHz/10 V/m Frequency / Field: 2700~5000MHz/10 V/m Frequency / Field: 5100~6000MHz/10 V/m |
||
Electrical Fast Transient/Burst Immunity Test | EN 50155 13.4.8 / EN 50121-3-2, EN 61000-4-4 | ||
Line, Neutral, Line+Neutral: ±2KVDC | Line, Neutral, Line+Neutral: ±2KVDC* | ||
Surge Immunity Test | EN 50155 13.4.8 / EN 50121-3-2, EN 61000-4-5 | ||
Line to Line: ±1KVDC | Line to Line: ±2KVDC* | ||
Radio-Frequency, Conducted Disturbances Immunity Test | EN 50155 13.4.8 / EN 50121-3-2, EN 61000-4-6 | ||
Frequency : 0.15 to 80MHz Field: 10 Vrms |
Frequency : 0.15 to 80MHz Field: 10 Vrms |
||
Power Frequency Magnetic Field Immunity Test | EN 61000-4-8 | ||
No Needed | Frequency: 50Hz Field: 30/100/1000 A/m |
||
Damp Oscillatory Magnetic Field Immunity Test | EN 61000-4-10 | ||
No Needed | Frequency: 0.1 & 1 MHz Field: 30 A/m |
End of Why is it necessary for a power converter to comply with the EN 50155 railway certification? (Part 1)
Thank you for watching. If you are interested, please refer to the next episode: Why is it necessary for a power converter to comply with the EN 50155 railway certification? (Part 2)
For more information,please click on the following links:
- 【MINMAX Railway Certified Products _ Power Solutions】
- 【MINMAX Railway Certified Products _ Product Selection Guidebook】
- 【MINMAX Railway Certified Product _Product Introduction Video】
- 【MINMAX Railway Certified Series _ Quarter Brick_MRZI150 Series】
- 【MINMAX Railway Certified Series _ 2" x 1"_MKZI40 Series】
- 【MINMAX Railway Certified Series _ DIP-24_MIZI03 Series】
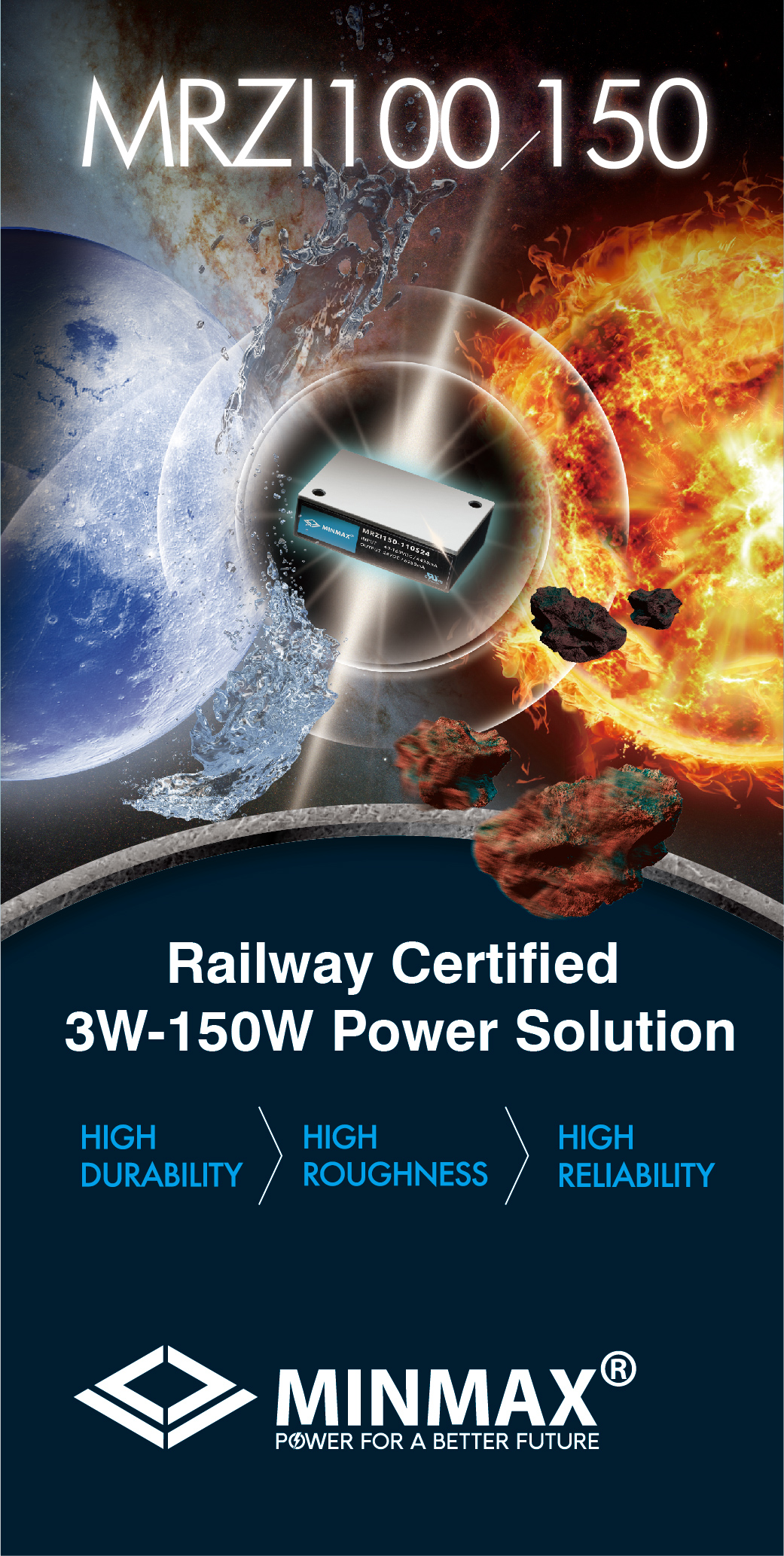